5 Conveyor Design Principles: An Engineering Approach
- Kyle O'Brien
- Jun 6
- 3 min read
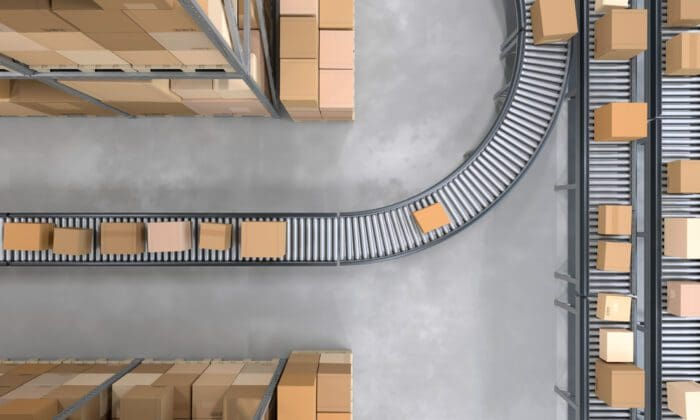
Conveyors remain one of the most effective material handling solutions in warehouse design, especially when:
You have high, predictable throughput, such as parcel sortation, case picking, or eCommerce fulfillment.
You need consistent, reliable flow across fixed paths or long distances, especially where flexibility isn't a core requirement.
While mobile robots offer flexibility and dynamic routing, conveyors shine when the operation demands high-speed, continuous transport and sortation. Below are five essential engineering principles for designing an effective conveyor system.
1. Match Conveyor Speed to Process Requirements
The conveyor must be designed to handle the peak flow rate, not just the average, without creating bottlenecks. This often means calculating the required feet per minute (FPM) based on product size and spacing.
Formula:
Speed (FPM) = (Cartons Per Hour * Gapping (in)) / (60 * 12)
Example:
To move 2,400 cartons/hour spaced at 30 inches:
Speed = (2400 * 30) / (60 * 12) = 100 FPM
Typical conveyor speeds:
Case conveyors: ~60–200 FPM.
Sorters: ~300–500 FPM.
Belt conveyors for bulk transport: Up to 600 FPM.
Faster speeds may increase throughput but can cause product instability and require more precise controls. Always balance speed, spacing, and product characteristics.
2. Minimize Conveyor Length and Complexity
Longer conveyors cost more, use more energy, and increase maintenance needs. Keep flows as short, straight, and simple as possible; avoid unnecessary curves and elevation changes. Every extra foot of conveyor should earn its place.
Best Practices:
Avoid excessive curves and elevation changes.
Use spaghetti diagrams to validate shortest routes.
Consider vertical conveyors or lifts instead of long horizontal runs when space is tight.
3. Plan for Accumulation Zones
No system runs at a perfect flow rate. You need buffers that can absorb upstream surges or downstream stoppages.
Rule of Thumb:
Provide 2–5 minutes of peak-flow accumulation before key bottlenecks (like pack-out or sorters).
Formula:
Accumulation Length (ft) = (Peak Rate (cartons/min)) * (Hold Time (min)) * (Product Length (in) / 12)
Example:
If your peak rate is 50 cartons/min, with 2 minutes of desired buffer and each carton is 18 inches long:
Accumulation Length = 50 * 2 * (18 / 12) = 150 ft
This helps maintain continuous operation and reduces the risk of jams.
4. Select Sortation Technology Based on Speed and Product Mix
Choosing the wrong sorter can lead to missed SLAs, damaged product, or costly redesigns. Always match the technology to the operation.
Sorter Type | Throughput | Best For |
Tilt-tray | 8k-12k/hour | Small parcels, eCom |
Shoe Sorter | 6k-18k/hour | Cartons, cases |
Crossbelt | 5k-20k/hour | High-speed, mixed-size SKUs |
Narrow-belt | 3k-8k/hour | Mixed polybags, cartons |
Paddle Sorter | 2k-6k/hour | Lightweight parcels, gentle handling |
Bombay Sorter | 4k-10k/hour | Apparel, polybags, flat items |
5. Design for Maintenance, Safety, and Scalability
A conveyor system must be easy to access, safe to operate, and able to adapt.
Design Guidelines:
Provide 3–4 feet of clearance for maintenance access
Include emergency stops, guarding, and lighting
Design with future expansion in mind (modular lanes, scalable controls)
Even the most efficient conveyor is useless if it’s unsafe or too difficult to maintain.
Final Thoughts
Conveyors still hold a critical place in modern warehouse automation—especially when engineered with clear principles in mind. By applying the right design models and balancing performance with operational reality, you can create a system that delivers speed, reliability, and long-term ROI.
Are you designing a new conveyor system? I’d love to hear what principles or challenges you've encountered.
Comments